For the testing of these e-drives, we implemented the data acquisition solution and evaluation for a large German automotive supplier. Power consumption and speed are relevant to evaluating the efficiency of electromechanical systems. Since the motors are permanently installed into vehicle body parts, often only the electrical current and voltage signals are all that’s available for quality testing.
Using the Current Signal to Determine Motor Speed
In a classic DC motor, the mechanical commutator leads to a brief drop in the current curve when poles are reversed. Depending on the design and number of poles of the motor, the quantity of current dips corresponds to one revolution. This model is also reflected in the current curve of brushless motors with electronic commutation.
Figure 1 demonstrates the current curve of a motor over time. The current pictured here was measured with a Q.bloxx XL A107 I/O module and a shunt. The current drops visible in this example occur during commutation at intervals of 8.4 ms.
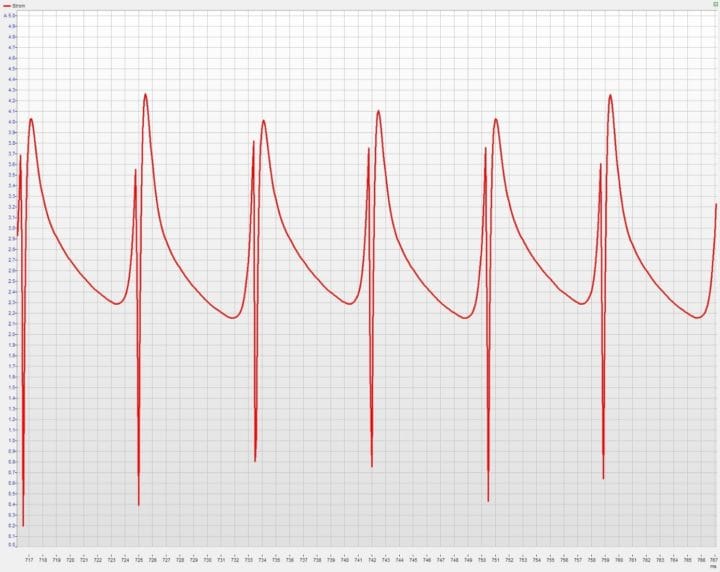
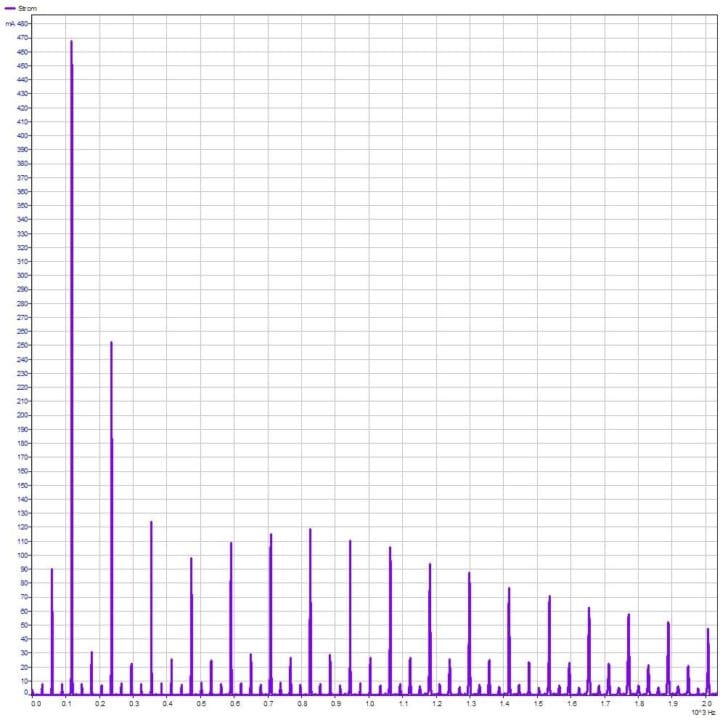
Accordingly, the spectrum of the current curve (Figure 2) shows its maximum occurs at 119 Hz. Assuming 3 commutations per revolution, this corresponds to a speed of 2380 revolutions per minute.
The spectrum can be performed both online and offline by Q.series X controllers. In this way, the engine speed can be determined continuously and live on the test bench using the current signal. The necessary configuration is performed in just a few steps.
Quick-and-Easy Configuration on the Test Bench
The FFT function of the Q.series X controller offers, among other things, the possibility to evaluate the maximum of a spectrum within a selected frequency band by magnitude and frequency. The frequency of the maximum corresponds to the fundamental wave and is divided by the number of poles and multiplied by 60 to give the speed in revolutions per minute (rpm). Also, the current is used to detect whether the motor is in operation and whether the electrical power can be calculated.
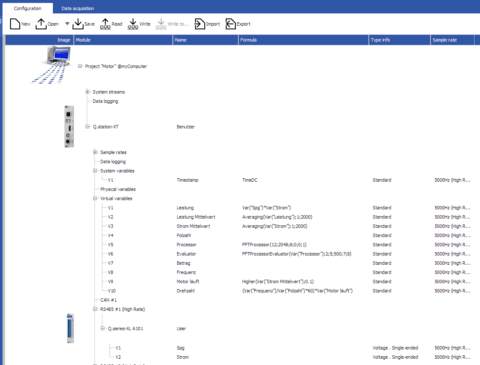
This edge computing allows the motor speed to be determined without a separate computer.
Depending on the test bench configuration, data can now be transferred to the system control, e.g., via EtherCAT or visualized within GI.bench on the test bench PC or over the local network.
Simply Powerful Visualization
With GI.bench, you can create custom dashboards for visualization. Figure 4 shows the speed and power in the upper chart. When the motor is loaded, the speed decreases (green curve), while the power consumed increases (grey curve). Also, the current spectrum (blue), the current trace (red), and the parameters (table) are displayed numerically in this interface.
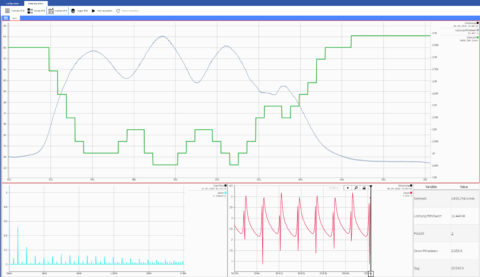
For references, demo programs and questions you can always contact us at info@gantner-instruments.com.
More articles
Austrian Railways Measurement Vehicle Detects Signal Magnets Using the Q.station Test Controller
The Austrian Federal Railways (ÖBB) continuously checks the quality of its network using special measurement vehicles. Measurement data is required as the basis for maintenance and renovation work; a precise geographic reference data is therefore important.
Read more...Test Like You Fly, Fly Like You Test
When building a rocket there is a whole flight certification process, and qualification is an important part of that. It proves the hardware meets the requirements and performs the way it is designed to do. Of all parts of a rocket, the engine section is perhaps the most critical during launch. The weight of the massive rocket is pushing down, while the engines are pushing up with millions of pounds of thrust. Whether it is an engine for experimental rockets or for commercial spaceflight, adequate testing is critical to the success of each launch program.
Read more...New Monitoring Solution – Q.series Portable
For short-term or rout-based condition monitoring of various assets we now provide a portable system solution. Our new Q.series Portable based on Q.station 101 and OEM-boards for analog and digital inputs contained in a robust transport case is fully engineered and ready to use ‘out of the box’. The electronic boards and the power supply system are mounted on shock absorbers to withstand heavy-duty work under harsh environments in the field.
Read more...